Basic Knowledge of Wire
Basic Concept
Wire is an essential medium for transmitting electrical energy, heat, and signals. In 1744, the German scientist J. Winkler achieved a breakthrough in the remote transmission of electrical energy through wires. Wires can be classified into different types, such as bare wires, magnet wires, and insulated wires.
Bare wires, which lack an insulation layer, include copper and aluminum flat wires, overhead stranded wires, as well as various profiles like profiled wires, bus bars, copper bars, and aluminum bars. These wires are primarily used for outdoor overhead applications, as well as indoor busbars and switch boxes.
Magnet wire, on the other hand, is an insulated wire that produces a magnetic field when energized or induces a current in the presence of a magnetic field. It finds extensive use in motor and transformer windings, as well as other electromagnetic equipment. The conductor in magnet wire is typically copper, which requires a thin insulating layer with excellent electrical and mechanical properties. This insulation should possess qualities such as heat resistance, moisture resistance, and solvent resistance. Different insulating materials can be chosen to achieve desired properties. The two main types of magnet wires are enameled wire and wrapped wire.
Enameled wire is created by coating bare copper wire with insulating varnish. The insulating layer is thin and occupies minimal space. Enameled wire is widely employed in various electrical appliances and instruments, with its properties varying depending on the type of insulating material used.
Wrapped wires encompass various types such as yarn-wrapped wire, silk-wrapped wire, glass fiber-wrapped wire, paper-wrapped wire, and plastic film-wrapped wire. Yarn-wrapped and silk-wrapped wires may be less desirable due to their poor temperature resistance and larger volume occupation. Glass fiber-wrapped wire consists of a round copper wire wrapped with glass fiber and impregnated with silicone resin. It exhibits excellent insulation performance, mechanical strength, and can withstand high temperatures up to 180°C. Paper-covered wires are mainly utilized in oil-immersed transformers. Plastic film-covered wire, on the other hand, involves coating the conductor with a polyimide film using adhesive and then undergoing a baking process. The resulting insulating layer is tough, elastic, easy to wind, wear-resistant, and heat-resistant. It finds wide-ranging applications in aerospace and other equipment.
Insulated wire generally comprises a conductive core, an insulating layer, and a protective layer. The wire core can be categorized into four configurations: hard, soft, mobile, and extra soft, depending on the specific usage requirements. Furthermore, wire cores can be classified as single core, two cores, three cores, or four cores. The insulating layer is typically made of rubber, plastic, or similar materials. Insulated wires are extensively employed in various instruments, telecommunication equipment, power lines, and lighting circuits operating at AC voltages below 500 volts and DC voltages below 1000 volts.
The cable industry is characterized by a wide range of subdivisions. Industrial cables and consumer cables are just one category among many, which also includes special cables and more.

Introduction to The Classification and Structure of Wire
The general structure of the wire is as follows:
Conductors generally include: copper wire, aluminum wire, copper-clad steel, iron wire, copper foil wire (Tinsel), etc.;
Insulation Jacket generally include: PVC, PE, PP, TEFLON, TPU, TPE, FPE, etc.;
Protective layer: armor (steel pipe), ceramic, polyester fiber, braided mesh, etc.
Copper
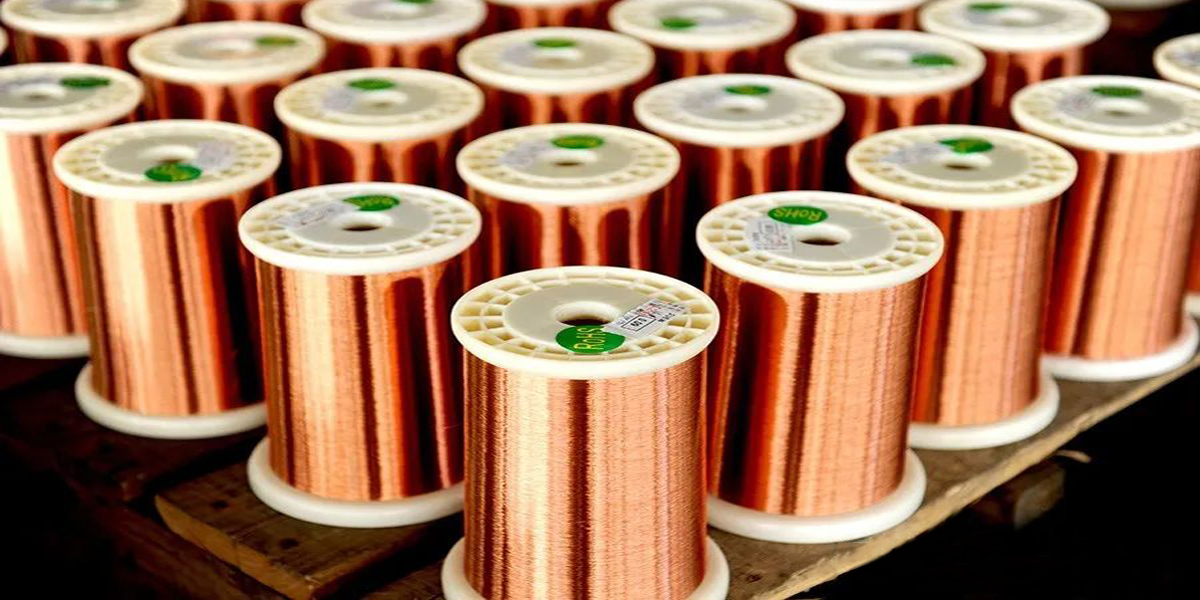
Copper wire classification
Generally Classified into:
■ Multi-strand wire (Strand)
■ Single-strand wire (Solid)
■ Tinned wire
■ Aluminum wire
■ Enameled wire
■ First twisted and then plated wire
■ Copper foil wire (Tinsel)
■ Multi-strand wire: which is the most commonly used.
The most wires use multi-strand wire, mainly for the following reasons:
Easy extrusion processing, making the wire soft;
Increase the cooling area;
Increase the tensile strength and flexural strength;
Reduce loss; (In large cross-section power cables, there is no need to split the conductor, and the current resistance of the cable will increase and the carrying capacity will decrease due to the skin effect and proximity effect).
The meaning of the usual copper wire code:
■Bare copper wire BA.AS or CU;
■ Tinned wire TAS, TCU or TS;
■Twisted first and then plated TC-T;
■ Copper foil wire (TSL);
■Copper clad steel CCS, tinned copper clad steel CP;
■ Copper clad aluminum CCA, copper clad aluminum magnesium CCAM, etc.;
■Silver-plated copper wire SC;
■ Silver-plated copper-clad steel SCCS;
Insulation Jacket

The insulation and the outer cover mainly play a protective role. Plasticizers, flame retardants, antioxidants, coupling agents, anti-aging agents, and anti-ultraviolet agents are added to PVC to make the outer cover bear different functions.
The insulation thickness is different, the withstand voltage level is different: (1mil=1/1000inch=0.0254mm)
■Thickness less than 15mil, used below 150V such as UL1571
■Thickness less than 30mil, used for below 300V such as UL1007
■Thickness less than 45mil, used for below 600V such as UL1015
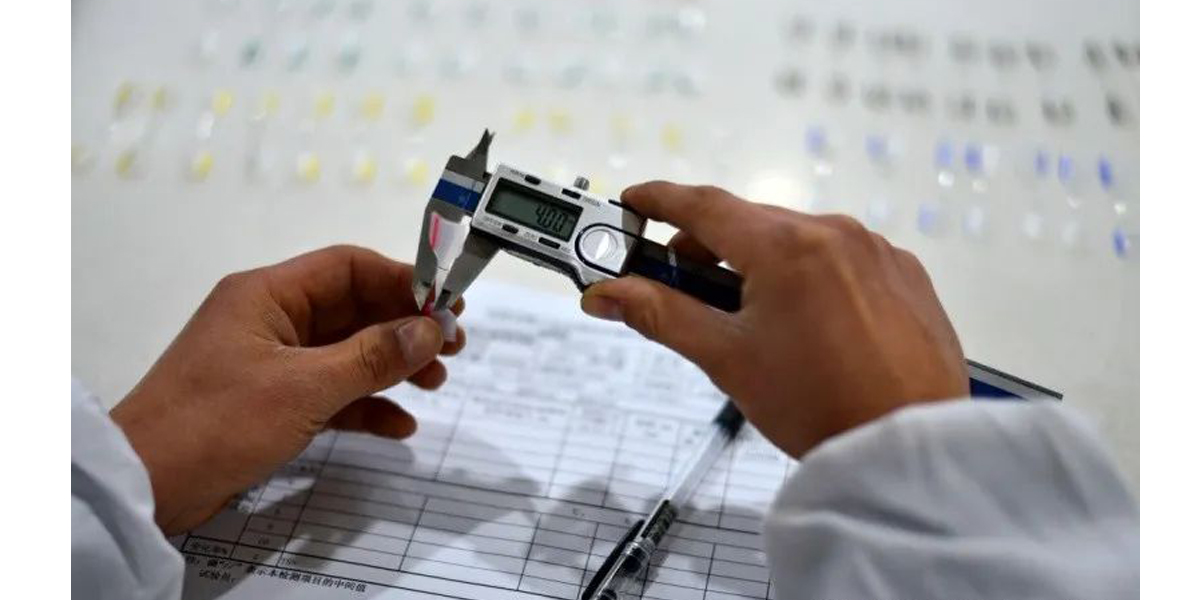
Heat resistance refers to the ability of a conductor to withstand elevated temperatures for a specific duration without degrading. Different types of insulation materials determine the heat resistance level of wires. For instance, wires with a temperature rating of 80°C (such as UL1007, UL2464, etc.) can withstand that temperature. When flame retardants are added, the temperature resistance can increase to 105°C (e.g., UL1015, UL1672, etc.). Insulation materials like XLPVC (cross-linked polyvinyl chloride) can provide temperature resistance ranging from 105°C to 125°C, as seen in wires like UL1430 and UL1431. XLPE (cross-linked polyethylene) insulation enables wires to withstand temperatures up to 125°C, as found in UL3271 and UL3266 wires. Silicone rubber insulation can withstand temperatures up to 150°C, seen in wires such as UL3122 and UL3135. Tetrafluoroethylene (TEFLON) insulation offers an even higher heat resistance of 200°C to 260°C, seen in wires like 1330.
MI cable (mineral insulated cable) consists of a copper core, copper sheath, and magnesium oxide insulation. It exhibits excellent fire-resistant properties, allowing it to operate for prolonged periods at temperatures below 250°C.
Furthermore, some special wires are coated with a layer of mica tape, enabling them to withstand extremely high temperatures above 800°C for 90 minutes. These wires are known as true fire-resistant cables.
Wire Color Definition
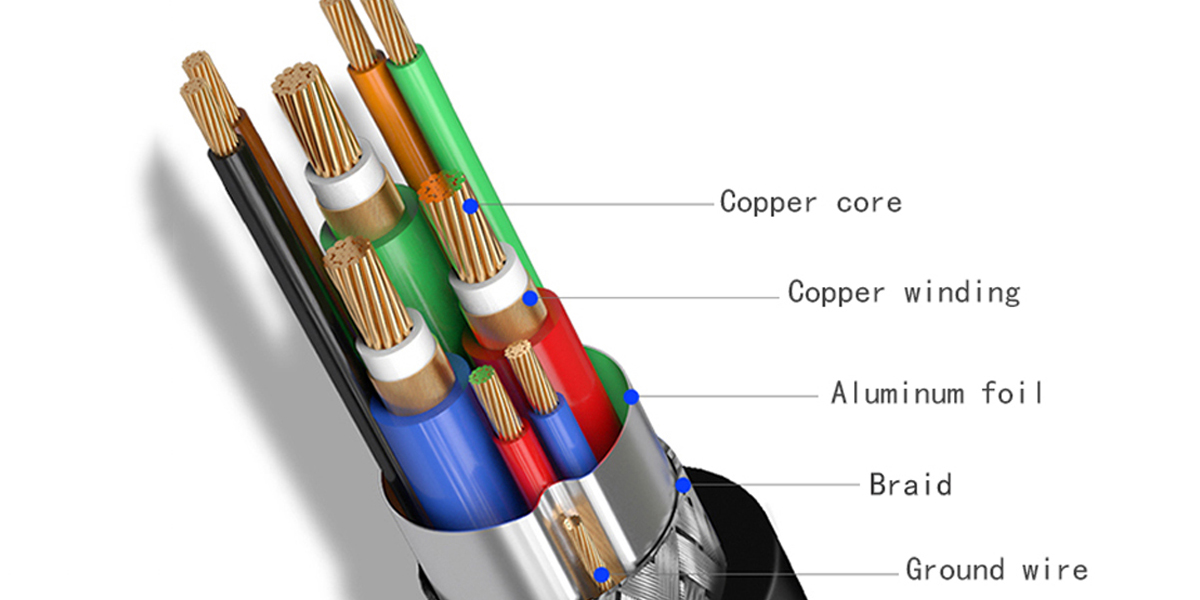
Main color of electronic wire: black, brown, red, orange, yellow, green, blue, purple, gray, white, pink, light blue, light gray.
Communication cable pair main-auxiliary color:
a) Line (main color): white, red, black, yellow, purple
b) Line (auxiliary color): blue, orange, green, brown, gray multi-logarithmic based on primary and secondary colors:
Other wire colors
Mainly in accordance with the requirements of wire standards or association standards (such as ICEA Insulated Cable Engineer Association, and Western European electronic standards WesternElectric, etc.).
North American AWG system: Black (L) White (N) Green (E) Red (4) Yellow (5) Orange (6)
European Harmonized System: Brown (L) Blue (N) Yellow/Green (E)
Or except for the ground wire which is yellow/green, all are black, and each wire is printed with 1, 2, 3, 4, etc. or the color standard formulated by the company for the convenience of unified management
Specific color standards refer to PANTONE, or RAL 840 HR and RAL841 GL.
Or customer’s real sample color (see attachment 02 PANTONE Pantone color card, 03 RAL_German standard).
There is no regulation for the outer jacket (sheath) color, and it can be made according to user requirements.
IEC 757 regulations on color codes and abbreviations:
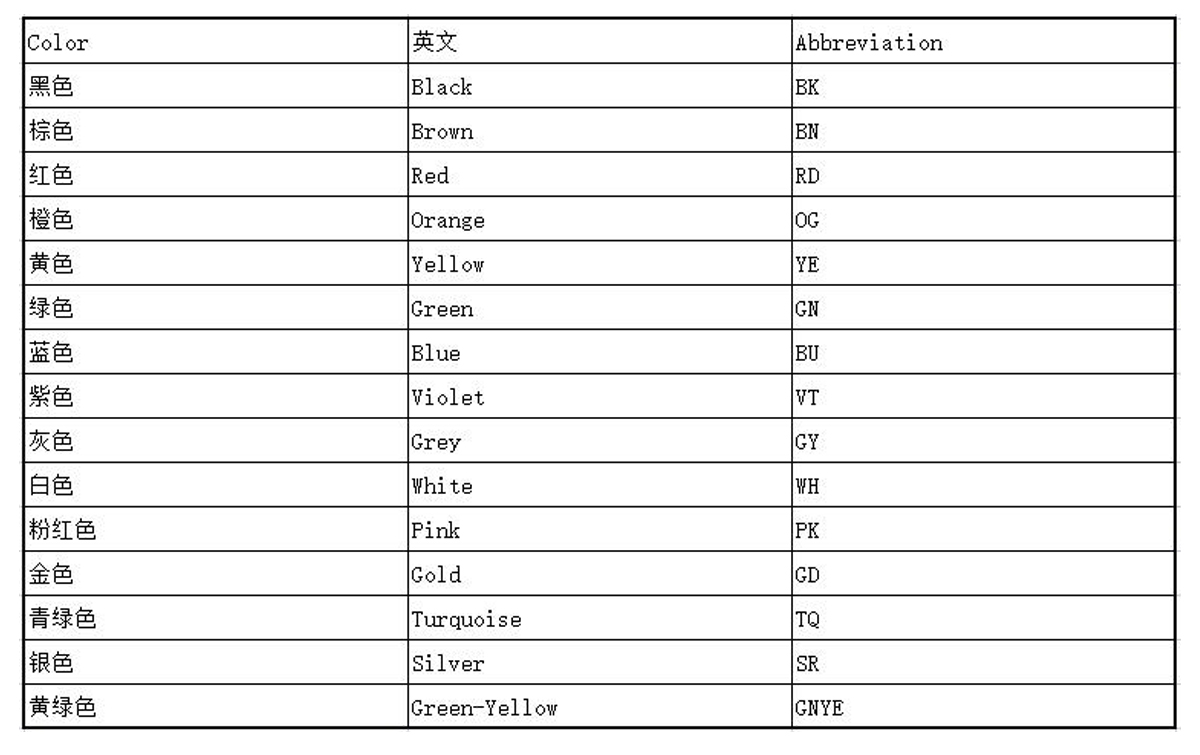
Classification of Wire
Classified by material (refer to UL758): For example, UL (Underwrite’s Laboratories) American Commercial Insurance Laboratory, the American national standard ANSI adopts 70% of UL standards as its standards:
Classified by safety standards:
CCC standard: China Electrical Equipment Certification Committee standard 3C logo as shown on the right, the wires we often use mainly include: BVR, RVV, RV, RVB, etc.;
UL standard: American commercial insurance laboratory standard, the logo is shown on the right. The wires we often use mainly include: UL1007, UL1015, UL1061, UL3266, UL3271, UL1330, SJTW#12*2C, UL2651, UL20276, UL2464, etc.
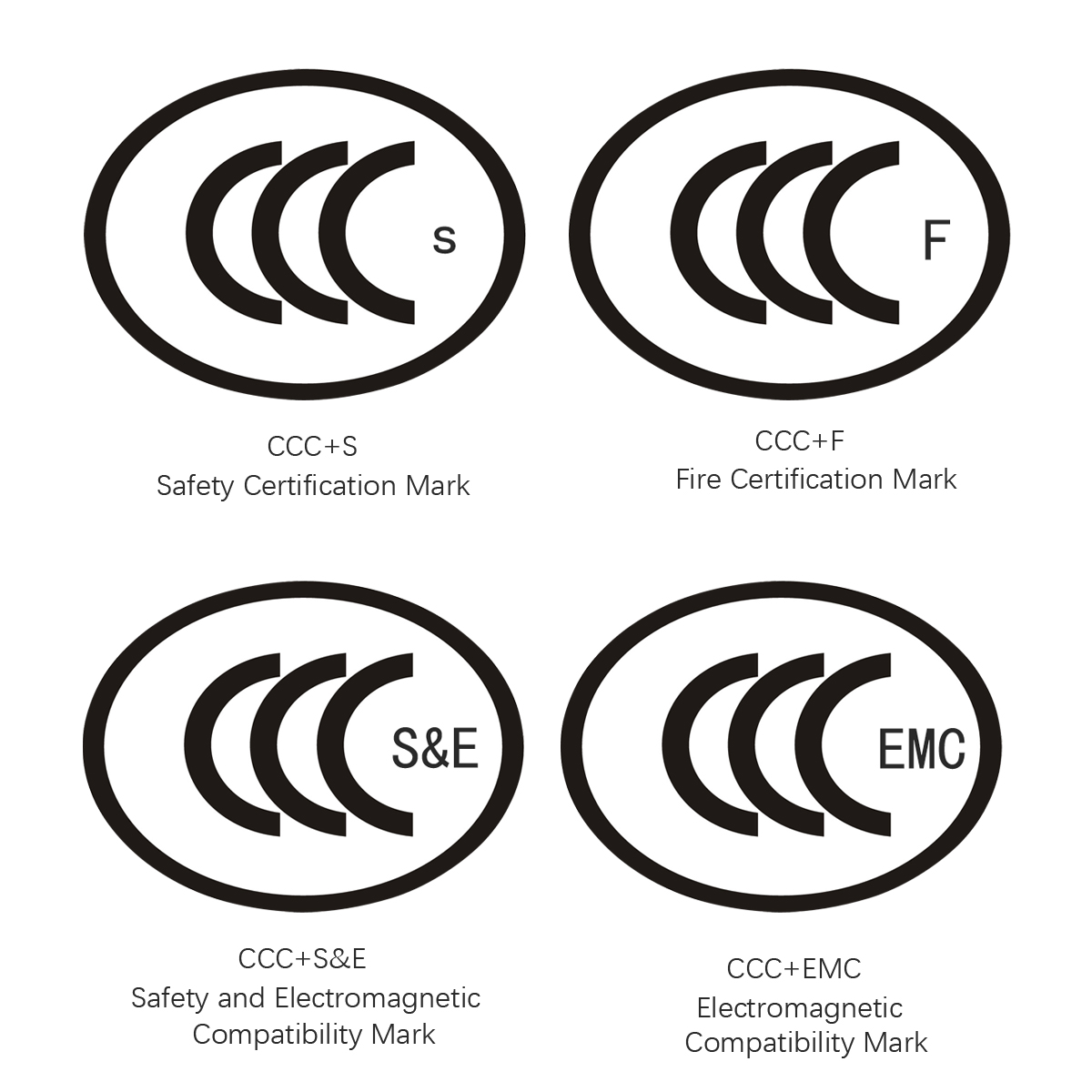
Classified by shape:
Round wire: such as UL1015, UL1007, SJTW#12/3C, SVT#18/2C, RVV3*1.5, etc.
Flat wire: such as FFC, UL2651, UL2468, SPT-3, RVVB, etc., see the table below:
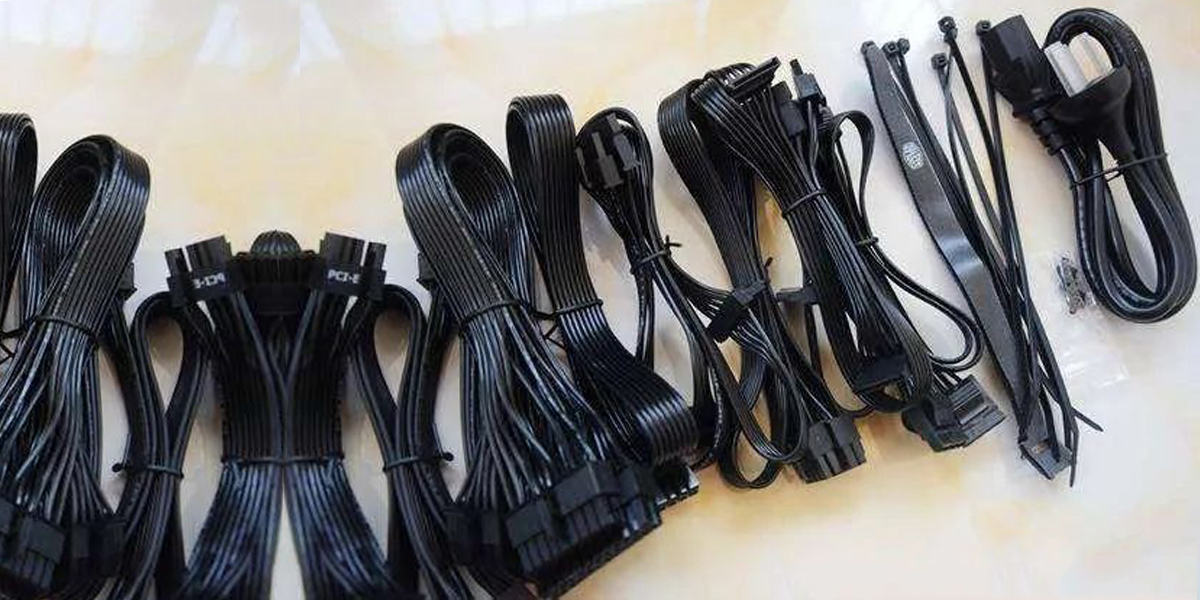
The Meaning of Wire Printing
The printed content should include: certification logo, certification code, wire gauge, wire number, pressure rating, heat resistance rating, fire rating, etc.
Description of UL printed content:
AWM: American Wire Gauge;
1015: model number;
VW-1: UL vertical resistance 105°C: rated temperature;
E****: UL certification number;
AWG18: wire number;
CARVE: supplier;
600V: rated voltage;
CSA LL**** : Canadian Certification Number
TEW 105: Canadian model;
FT1: CSA vertical flame retardant.
(AWM: appliancewiring material; AWG: American Wire Gauge; CSA: Canadian Standards Association)
There are also some I/II, A/B and other words that represent the following meanings: Class I is used internally, Class II is used externally
Group A is not subject to mechanical wear, Group B is subject to mechanical wear, W is used in a humid environment, O is oil-proof, F is fuel oil-proof, etc., FT1 vertical burning test, FT2 horizontal burning test, FT4 vertical burning test, FT6 horizontal burning and smoke test.
CCC standard, China Electrical Equipment Certification Committee standard:
picture
1) CCC: the abbreviation of China Compulsory Certification (China Compulsory Certification);
2) 227 IEC 06: meet the requirements of 227 IEC 02;
3) R: soft wire;
4) V: PVC insulation;
5) 300/500: line voltage/phase voltage;
6) 1*Size MM^2: 1 square wire;
7) CHAU’S: Supplier LOGO;
8) CQC
9) 2002010105011353: 3C certification number of the wire factory;
10) GB5023-97: National Standard 5023-97
Non-UL wire structure, generally no printing, wire specifications are described as follows:
3COAX(B)*28AWG+(1P*28AWG+D+AL+Mylar)*4C+1P*28AWG+5C*28AWG+AL+B
1) COAX: coaxial cable;
2) B (braid Shield): The shield is braided;
3) S (Spiral): winding;
4) AWG: American Wire Gauge;
5) P (Pair): pair twisted;
6) D (Drain): ground wire;
7) AL: aluminum foil;
8) Mylar: Mylar
Inspection, test, specification
Appearance inspection requirements:
■Smooth skin, no granulation, no unevenness;
■The printing is clear and meets the product printing requirements;
■No raw rubber, black, color difference, etc.
Conductor and core wire requirements:
The conductor structure meets the requirements of the core wire, and can be tinned or bare copper as required;
The average value of the insulation thickness is not less than the nominal value, and the thinnest point is not less than 90%-0.1mm of the nominal value; the average value of the sheath thickness is not less than the nominal value, and the thinnest point is not less than 85% of the nominal value- 0.1mm;
The stranding pitch (twisting pitch) of the multi-core cable should not be greater than 25 times the outer diameter of the stranding calculation, and the outermost layer is right-hand;
■The sheath and insulation cannot be bonded together; the signs of batches of cables should conform to reality and be clearly written, easy to identify and wear-resistant.
Guideline:
GB5023.1~7 Rated voltage 450/750V and below PVC insulated cables-1997.07.30
GB5023.1 General requirements
GB5023.2 test method
GB5023.3 fixed cloth wire without sheath cable
GB5023.4 fixed cloth cable sheathed cable
GB5023.5 flexible cable (flexible wire)
GB5023.6 Cables for flexible connection of elevator cables
GB5023.7 2-core or multi-core shielded and unshielded flexible cables
UL758/2010 Electrical wiring wires and cables and their test methods
UL1581-2001 Reference Standard for Wire, Cable and Flexible Cords