Summary of Popular Science on Common Cable Materials
With the development of global industrialization, there are more and more high-speed and high-frequency application scenarios, and the natural environment is constantly being eroded by disasters. Resource issues have become a top challenge for the development of various industries. The production and manufacturing process of cables also puts forward new requirements for the application of insulation materials. Environmental protection concepts such as circular economy and low energy consumption products have also been injected into the application of wire and cable insulation materials. How to choose appropriate materials has become crucial, Today we have compiled and summarized commonly used cable plastic materials to share with everyone. Cable insulation plastics used for wires are generally relatively light, with a physical relative density of about 0.83~2.2, and most of them are between 1~1.5. The following is a list of the specific gravity of commonly used rubber and plastic materials for wires (as a reference). The elongation and tensile strength of each insulation vary depending on the type of wire used and its rated temperature, So for reference only (all pre aging requirements), please refer to the corresponding UL. IEC and other safety regulations during actual operation. For example, UL444 is the safety code for communication cables, UL758 is the safety code for AWM cables, UL1581 is the general safety code for general cables, and UL62 is the safety code for POWER CABLES.
Introduction to Common Plastic Materials for Cables
PVC (Poly Vinyl Chloride)
(1) Various hardness can be adjusted, transparent or opaque. Transparent hard PVC is added with plasticizer (DOP. DIDP. TOTM) to form soft PVC.
(2) Advantages: Suitable for high and low temperatures, flame resistant, good softness, and low unit price.
(3) Disadvantages: PVC has poor heat resistance. Its dielectric coefficient can vary depending on temperature and frequency, making it difficult to control its electrical characteristics. Heating can remove hydrochloric acid and turn it black. During combustion, there is a pungent smell of black smoke and carbon residue, which does not support combustion. Toxic gases are generated during combustion.
(4) Purpose: Used for AWM and computer cables with voltages below 600V, mostly using PVC Specific gravity (wire insulation or outer covering material): 1.20~1.50.
The specific gravity of PVC and polyvinyl chloride (soft): 1.2; Specific gravity of PVC and polyvinyl chloride (hard): 1.4; The dosage is usually calculated based on a specific gravity of 1.5; Elongation rate 150-400%, tensile strength 1.2-1.5kg/mm2 (1kg/mm2=1422PSI).
UL758.1581 Safety requirements: AWM type wires have an elongation rate of 100% min and a tensile strength of 1500PSI min.
UL444 safety regulations require communication cables to have an elongation rate of 100% min and a tensile strength of 2000PSI min.
How to identify PVC materials? When burning, green light covers the area, green flames, and yellow flames roll out, and white smoke and hydrochloric acid taste are emitted after combustion. Generally, flame-retardant PVC will self-extinguish.
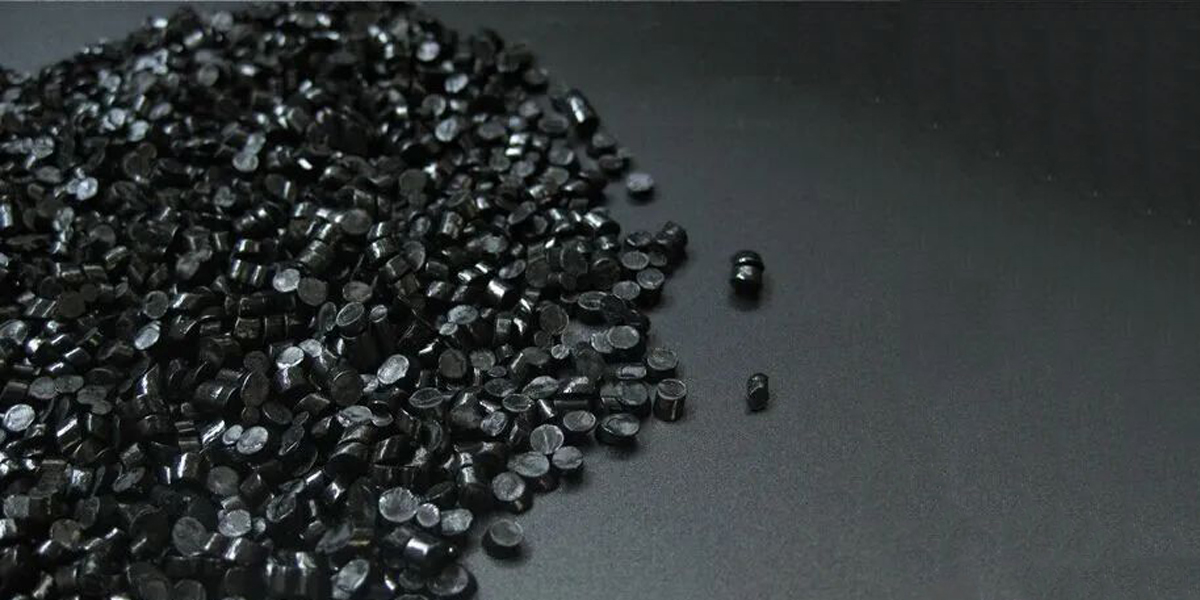
SR-PVC (Semi Rigid Poly Vinyl Chloride)
(1) Advantages: The strength is greater than that of regular PVC
(2) Disadvantage: Due to its high hardness, the elongation will decrease after high-temperature aging
(3) Purpose: Generally used as insulation material for computer wires
Density: 1.35-1.50; The dosage is usually calculated at 1.5
UL1581/UL444 safety requirements: elongation rate 100% min, tensile strength 3000PSI min
How to identify SR-PVC materials?
SR is a semi hard PVC, which is harder than regular PVC and has higher requirements for tensile strength. The flame retardant judgment standard is actually the same as PVC, and is generally used in the design of UL1061 thin core wires.
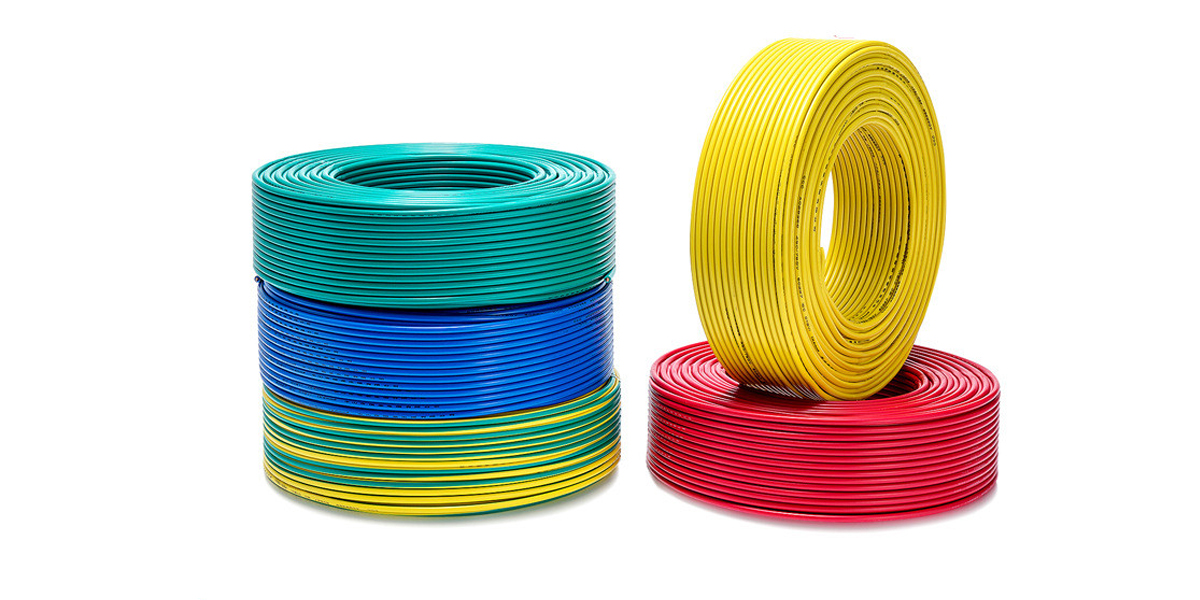
PP (Polypropylene)
(1) PP is a rapidly developing and widely used thermoplastic
(2) Advantages: Compared with other general-purpose thermoplastic plastics, PP has the advantages of small specific gravity, good rigidity, high strength, resistance to bending, heat resistance above 100C, good chemical corrosion resistance, and low price
(3) Disadvantages: Poor low-temperature impact resistance, easy aging, high molding shrinkage, flame droplets during combustion, difficult to extinguish, rapid and complete burning, and delayed combustion
(4) Usage: PP+EVA is used as insulation material for the core wire of electric wires, generally used for communication cables and telephone lines
Specific gravity is 0.90~0.91
Elongation rate 200-700%, tensile strength 2.0-4.0kg/mm2 (1kg/mm2=1422PSI)
UL1581 Safety Requirements: Elongation rate 150% min, tensile strength 3000PSI min
How to identify PP materials, burning with blue flame light, melting and transparent combustion zone, with sol dripping and kerosene smell, is a ductile plastic that can continue to burn.
The most commonly used mask recently is the nose bridge strip of KN95, which mostly uses PP insulation as the extrusion material.
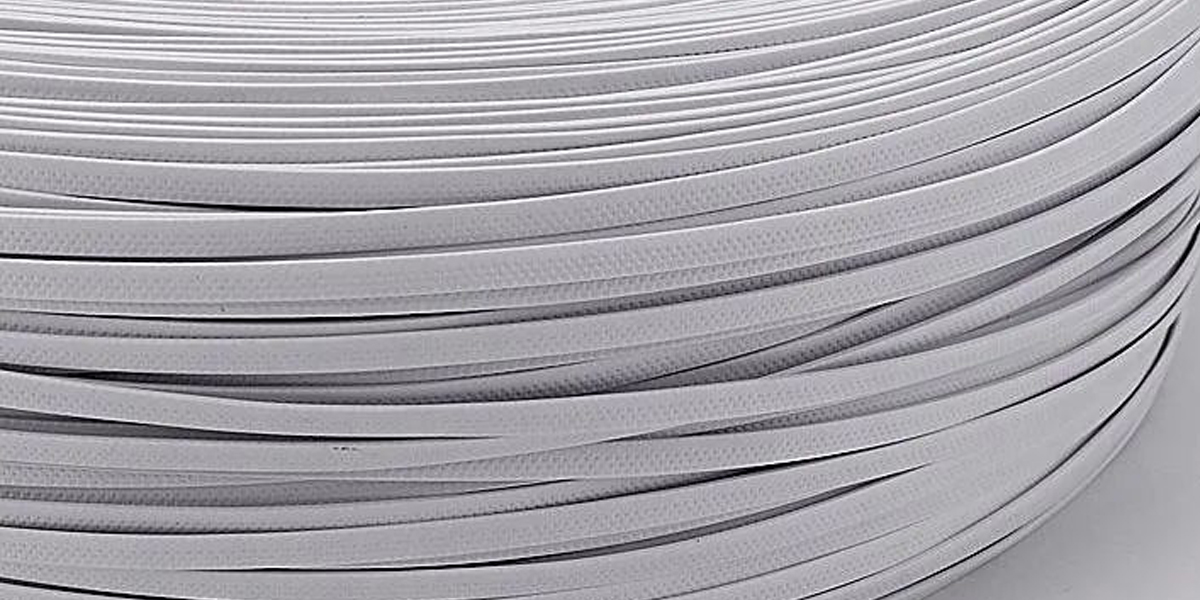
PE(Polyethylene)
(1) PE can be specifically divided into:
HDPE (High Density PE)
MDPE (medium density PE) is not widely used
LDPE (Low Density PE)
LLDPE (Linear Low Density PE)
FRPE (Flame retardant PE)
Cellular or FOAM PE
XL-PE (cross-linked PE)
(2) Advantages: PE is lighter than water, soft, water resistant, cold resistant, wear-resistant, and has excellent electrical characteristics
(3) PE is easily not extinguished, not heat-resistant, and will rapidly age at high temperatures
(4) Usage: Generally used for communication twisted pair cables, high-frequency coaxial cables, high-voltage cables, submarine cables, outdoor self-supporting cables, wires, communication cables, etc.
How to identify PE materials, burning blue flame light, melting transparent in the combustion zone, with the smell of sol dripping and candles, is a ductile plastic that can continue to burn.
HDPE(High Density Polyethylene)
(1) High density polyethylene is produced by low-pressure method, hence it is also called low-pressure polyethylene.
(2) Advantages: (a) Chemical resistance (b) Good electrical characteristics.
(3) Disadvantages: (a) Poor heat resistance, (b) Relatively low physical properties, (c) Soft surface.
(d) It has a high coefficient of thermal expansion and is easy to fail under mechanical and thermal pressure. The specific gravity is 0.94~0.97.
Elongation rate 100-400%, tensile strength 1.0-2.0kg/mm2 (1kg/mm2=1422PSI).
UL444 safety requirements: elongation rate 300% min, tensile strength 2400PSI min.
LDPE(Low-Density Polyethylene)
(1) Traditional low-density polyethylene is produced by free radical polymerization of polymer grade ethylene with oxygen or peroxide as an initiator at high temperature and pressure, hence it is also known as high-pressure polyethylene
(2) Advantages (a) Low specific gravity (b) Chemical resistance (c) Impact resistance
(3) Disadvantages: (a) very low strength/rigidity (b) poor heat resistance (3) high coefficient of thermal expansion and easy to fail under mechanical and thermal pressure
The specific gravity is approximately 0.91~0.93
Elongation rate 350-700%, tensile strength 1.0-2.0kg/mm2 (1kg/mm2=1422PSI)
UL444 safety requirements: Elongation rate 350% min, tensile strength 1400PSI min.
LLDPE(Linear Low Density Polyethylene)
(1) Compared with ordinary low-density polyethylene, it consumes less energy and has a higher yield. Especially, its physical and chemical properties are much better than ordinary low-density polyethylene, and its applications are also quite extensive. Its price is relatively low, and its mechanical properties are good, such as tear resistance, puncture resistance, tensile strength, and environmental stress cracking resistance
The specific gravity is approximately 0.915~0.945
Elongation and tensile strength are higher than LDPE.
FOAM SKIN: Inner layer foaming, outer layer SOLID extrusion
Advantages: Foam can reduce the outer diameter and material usage, achieve the expected electrical characteristics and functions. Low capacitance, attenuation, high impedance, and outer layer is a non foaming insulator, maintaining good rigidity and protecting the foam from deformation.
Disadvantages: Poor adhesion, welding wire shrinkage, non circular shape, unstable electrical characteristics. If it is SKIN FOAM (SOLID) and FOAM is outside, the adhesion is enhanced, and the welding wire will not shrink
No requirements for elongation and tensile strength.
SKIN FOAM SKIN: SOLID+FORM+SOLID
Advantages: Good adhesion. Welding wire has good heat resistance
Disadvantage: It requires the use of dual head extrusion, making operation difficult
The specific gravity of foamed PE is about 0.55-0.7, and its specific gravity varies depending on the degree of foaming
No requirements for elongation and tensile strength.
XL-PE (Cross linked PE) cross-linked PE
(1) Crosslinked insulation has emerged as the dominant choice for power cables, replacing oil-paper insulation and gradually displacing PVC plastic insulation. While there are various types of crosslinked insulation, they can be primarily categorized into two groups: physical crosslinking and chemical crosslinking, both offering consistent insulation quality.
Physical Crosslinking (Amplitude Crosslinking):
Advantages:
Exhibits excellent insulation quality, high degree of crosslinking, and superior weather resistance.
Well-suited for flexible wires, equipment wires, high-temperature (105°C and above), and flame-retardant wires and cables.
Disadvantages:
Uneven illumination, requiring repeated irradiation during production.
Not suitable for power wire production due to potential space charge injection into the insulation caused by excessive cable bends.
Chemical Crosslinking:
a) High-Temperature Crosslinking:
Includes steam and dry crosslinking methods.
Steam crosslinking is suitable for cables below 1KV due to its moisture content of 2000×10-6 in insulation.
Dry crosslinking, with a moisture content of (100-200)×10-6 in insulation, finds extensive use in 10-500kV cables.
b) Low-Temperature Crosslinking (Silane Crosslinking or Warm Water Crosslinking):
Involves crosslinking cables in warm water (70°C-90°C) or high humidity air, thus earning the name “warm water crosslinking.”
The crosslinking agent (silane) reacts with the linear structure of PE insulation in the presence of water, forming a network-like crosslinking structure.
The moisture absorbed becomes a part of the insulation molecules, resulting in a very low moisture content of (100-200)×10-6.
Warm water crosslinking is typically suitable for 10kV and below cables, particularly 1kV warm water cross-linked cables, where thicker PE insulation prevents moisture penetration.
Warm water crosslinked insulation offers excellent product quality, low equipment investment, and fast production speed, making it an ideal cable product. Various crosslinking processes exist, including the two-step method, copolymer production method, monosil one-step method, and other derived process methods, with a total of seven production processes, including the solid-phase one-step method and blending method. Familiarity with these processes helps in purchasing high-quality cables.
Crosslinked cables provide high insulation quality, with a high-frequency breakdown strength of 50kV/mm and a dielectric constant of 2.3, making them an ideal choice for cable insulation. They boast a working temperature of up to 90°C, along with excellent heat and weather resistance, mechanical strength, and resistance to corrosion. In the realm of low to medium cable products, crosslinked cables are widely used. Despite variations in the crosslinking process, their insulation quality remains consistently high.
XL-PE (crosslinked polyethylene) has a specific gravity of about 0.9-1.0 and an elongation of 350-600%, maintaining the intended meaning while presenting distinct content from other articles.
Tensile strength 1.5-2.5kg/mm2 (1kg/mm2=1422PSI)
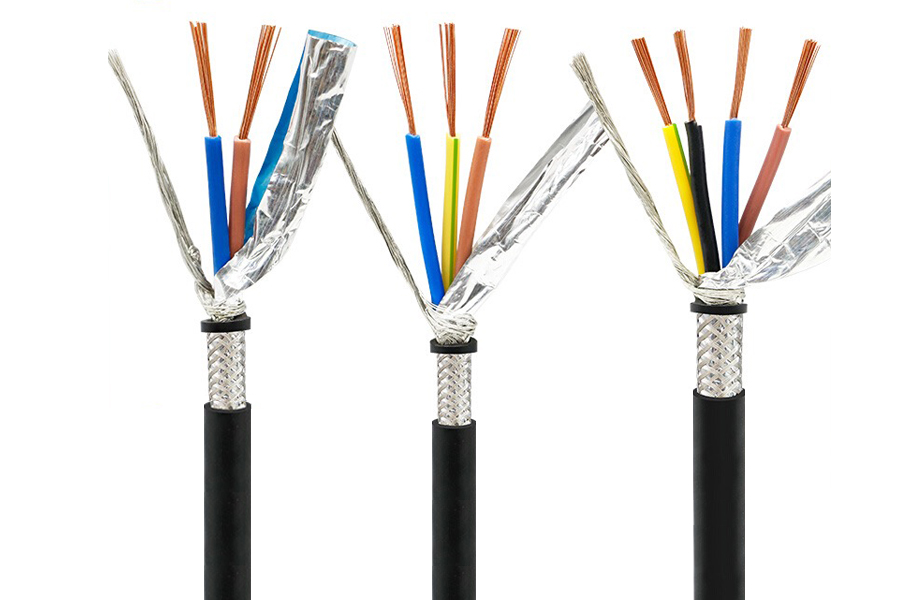
CPE (Chlorine Polyethylene)
(1) Chlorinated polyethylene is made from polyethylene (PE) by chlorination
(2) Advantages: It has the dual advantages of plastic and rubber, with superior oil resistance, ozone resistance, heat and oxygen aging resistance, corrosion resistance, flame resistance, bacterial and microbial resistance, and weather resistance compared to other rubbers. It can be used alone or blended with plastics and rubber.
Adding an appropriate amount of CPE to the wire and cable sheath can improve the flame retardancy, aging resistance and physical and mechanical properties of the cable sheath, and CPE with excellent performance can also be used as a wire and cable covering material.
(3) Usage: It has outstanding advantages in applications such as waterproof rolls, plastic doors and windows, wire and cable sheaths (most of the cables used for air conditioning are CPE sheathed rubber wires), rubber hose tape, colored bicycle tires, shaped parts, glass door and window sealing strips, etc. It is a hypothetical polymer elastic material with broad application prospects, with a specific gravity of 1.6.
UL1581 requires an elongation of 150-250% min and a tensile strength of 1200-1500 PSI min
It has excellent flame retardancy and has combustion and anti dripping characteristics, without flame dripping.
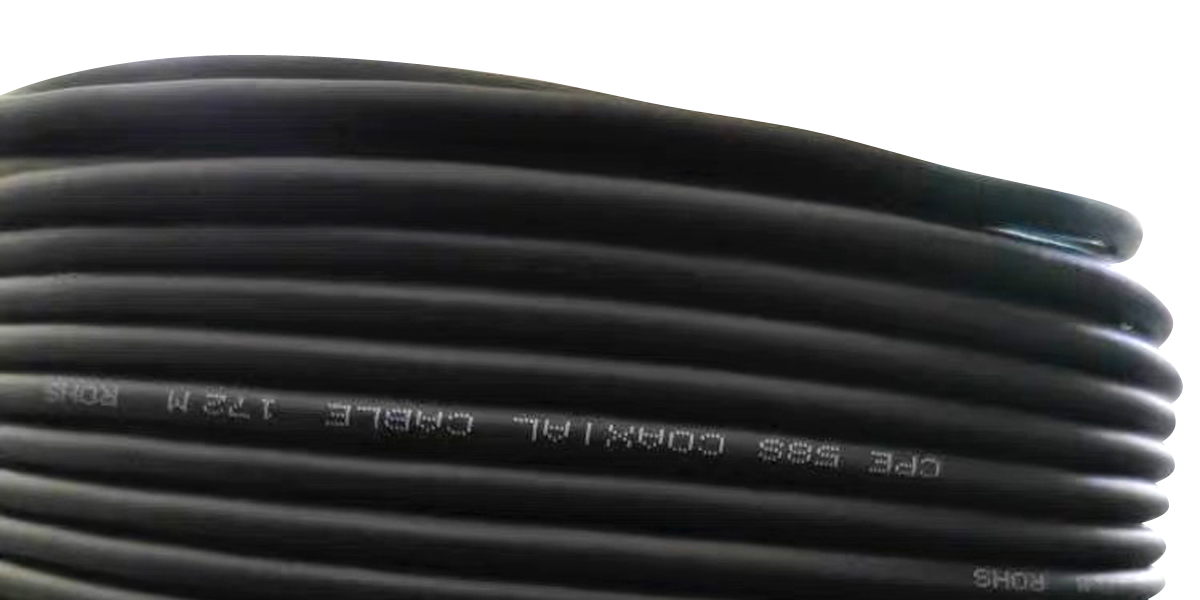
TPEE(Hytrel polyester elastomer)
TPEE, also known as thermoplastic polyester elastomer or Hytrel in Chinese, is a polymer composed of a rigid segment typically made of polybutylene terephthalate (PBT) polyester, and flexible segments made of aliphatic polyester or polyether. It is classified as a novel thermoplastic elastomer, characterized by excellent rubber elasticity and thermoplastic properties. TPEE is produced through transesterification and polycondensation of terephthalic acid, BDO, and PTMGE.
Distinguished by its remarkable mechanical strength, exceptional elasticity, impact resistance, resistance to creep, cold resistance, resistance to bending fatigue, oil resistance, chemical resistance, and protection against solvent corrosion, TPEE stands out as a high-performance engineering elastomer. It offers versatility in processing, allowing for adjustability in softness, hardness, and free design. Furthermore, TPEE can be further enhanced through filling, reinforcement, and alloy modification. This multifaceted material finds extensive application across various industries, including automotive components, hydraulic hoses, cables and wires, electronic appliances, industrial products, stationery, sports goods, biomaterials, and more. Its potential was initially underappreciated, but it has gained recognition as a relatively new elastic material.
Previously, TPEE was predominantly imported due to its limited domestic application and excellent material performance, leading to a relatively high price. As a result, TPEE was positioned as a high-end product with relatively niche usage, particularly in areas where exceptional product performance outweighs price considerations, such as military or bio-related materials.
The exceptional performance attributes of TPEE encompass various features, including outstanding high-temperature and low-temperature performance, impressive resistance to bending, excellent oil and wear resistance, remarkable biocompatibility, waterproof and breathable properties, and compatibility with other materials. While the core meaning of the statement remains unchanged, the content provided here is distinct from other articles.
Each performance characteristic presents potential opportunities in the market. Currently, the most common application for TPEE is in cables, where mechanical strength, corrosion resistance, wear resistance, thin insulation, and high flexibility are sought after.
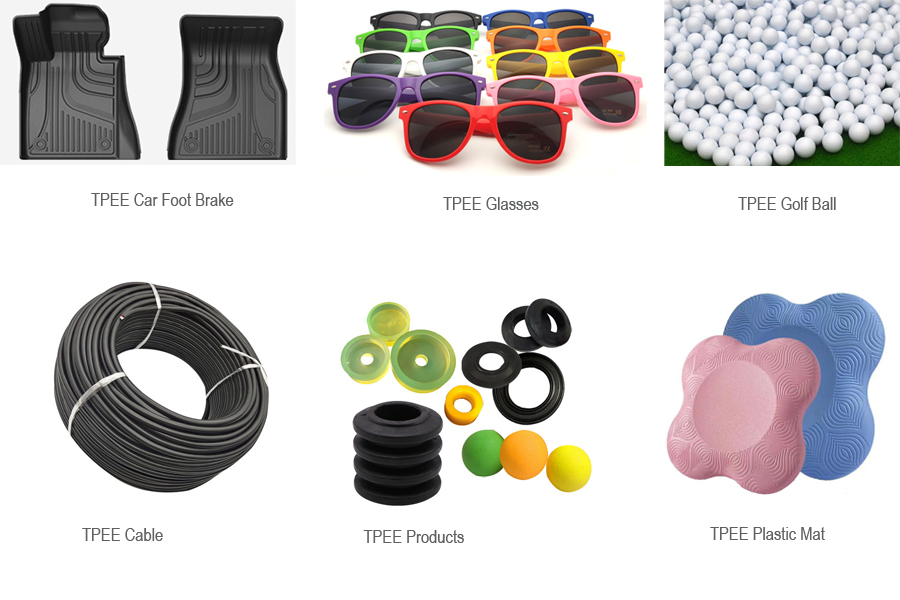
(1) Hytrel is the world’s best-selling thermoplastic polyester elastomer Hytrel isDuPont thermoplastic polyester elastomer is a registered trademark. This copolymer of polyether and ester combines the characteristics of most high-performance elastomers and flexible plastics
(2) Advantages: Excellent mechanical strength, corrosion resistance, wear resistance, and flexibility
(3) Disadvantages: High unit price, difficult to process
(4) Purpose: For thin insulation and high winding performance
The specific gravity is around 1.2
Elongation rate is about 350~550%, tensile strength is 4000~6600PSI.
PU (Polyurethane) polyurethane
TPU material: TPU is a kind of thermoplastic elastomer, which is formed by the polymerization of specific monomers, thus creating its unique characteristics, making TPU widely used in many types of products.
We use TPU wires and cables, This series is perfect for extrusion grade cable sheath applications: polyether (ISO10993-5/10 biocompatibility): can be used for medical equipment wires, skin contact wires, monitoring equipment, ultrasound imaging wires; Polyethers: Good hydrolysis resistance, low-temperature flexibility, microbial resistance, mold resistance, and low water solubility; Widely used in industries such as robot arm cables, submarine cables, charging pile cables, drag chain cables, geophysical cables, etc; Polyether flame retardant category: (UL 94-V0) high transparency, yellowing resistance, high mechanical strength, easy processing, color matching, widely used in industries such as charging pile cables, mining geophysical cables, automotive and ship cables, new energy wires and cables; Polyester: Good oil and chemical resistance, wear resistance, added with special hydrolysis resistant agents, with certain hydrolysis stability, high transparency, yellowing resistance, and easy processing. Widely used in production lines, data lines, headphone lines, consumer electronics lines, etc;
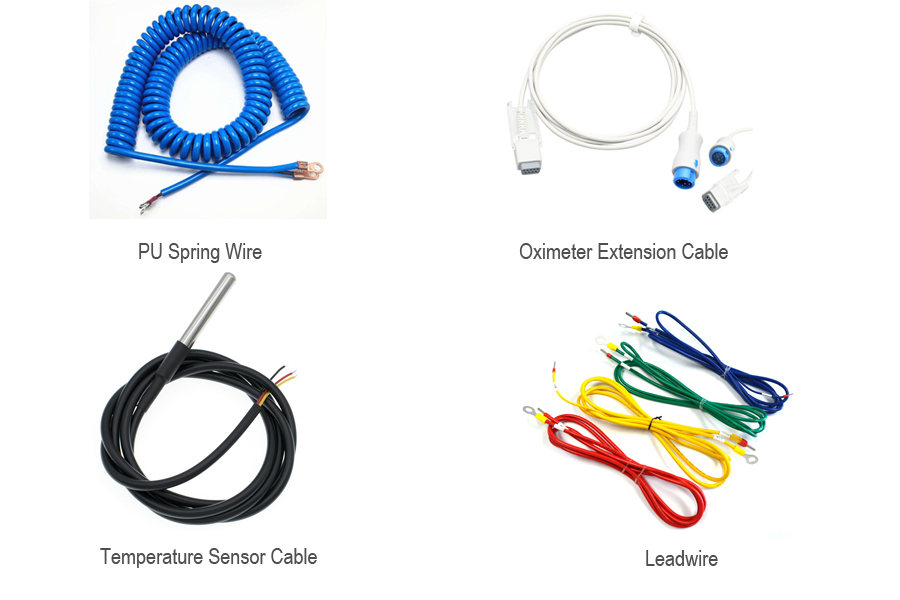
(1) Advantages: Temperature resistance -55~75c. Excellent mechanical strength, chemical resistance, electrical characteristics, weather resistance, and elasticity
(2) Disadvantages: High unit price, 2-3 times more expensive than PVC. Low flame retardancy and flame droplets during combustion, strong adhesion, and difficulty in peeling processing.
(3) Usage: Soft for elastomers, hard for insulating materials (For example, PU is used as a material outside the BOSCH automotive line).
Specific gravity is 1.0~1.2.
Elongation rate 500% min, tensile strength 30MPA min (1MPA=145PSI)
How to identify PU materials? When burning, there is black smoke, a blue flame, which is easy to melt, and there is a burning smell of hair, which has strong ductility.
PFA Fusible PTFE
(1) Also known as “perfluoroalkoxy fluoroplastics”, like PTFE, it is also perfluorinated fluoroplastics.
(2) Advantages: It maintains all the excellent performance of PTFE. Unlike PTFE, PFA can be melted at lower temperatures.
(3) Disadvantage: PFA is relatively expensive.
(4) Usage: Usually only used for special heating cables, thermocouples, and automotive high-temperature cables.
Specific gravity is 2.14
UL444 safety requirements: elongation rate 200% min, tensile strength 2500PSI min
How to identify Teflon materials, which soften and deform when exposed to fire, have a curved thin layer, a slight burning smell of coke, are non flammable, and soften when exposed to fire.
FEP (Fluorinated Ethylene Propylene) fluorocarbon resin
(1) It is a copolymer of TFE and hexafluoropropylene (HFP). It is also perfluorinated fluoroplastics.
(2) Advantages: Its resistance to chemical media is not inferior. Like PTFE and PFA, the insulation performance of FEP is also quite outstanding. It has inherent flame retardancy, low smoke emission, and easy processing.
(3) Purpose: FEP has become an ideal material for insulation of local area network (LAN) cables. It can withstand up to 205 ℃ and can be used as heating cables, thermocouples, automotive high-temperature cables, and high-frequency coaxial cables.
The specific gravity is between 2.0 and 2.2.
Elongation rate 100-300%, tensile strength 2.0-3.0kg/mm2 (1kg/mm2=1422PSI)
UL444 safety requirements: elongation rate 200% min, tensile strength 2500PSI min
How to identify Teflon materials, which soften and deform when exposed to fire, have a curved thin layer, a slight burning smell of coke, are non flammable, and soften when exposed to fire.
ETFE (Ethylene tetrafluoroethylene copolymer)
(1) Advantages: The strongest fluorine plastic has excellent scratch resistance and wear resistance. ETFE can also withstand high temperatures of 150 ℃, and the cross-linked ETFE can withstand high temperatures of 200 ℃.
(2) Disadvantage: It is one of the most difficult to process fluoroplastics
(3) ETFE is mainly used for wires and cables that require flame retardancy, low smoke generation, chemical resistance, as well as scratch and wear resistance, such as automotive, aviation, and heating cables
The specific gravity ranges from 1.7 to 1.73
Elongation rate 420~440%, tensile strength 0.7kg/mm2 (1kg/mm2=1422PSI)
UL444 safety requirements: Elongation rate 100% min, tensile strength 5000PSI min (150oC).
How to identify Teflon materials, which soften and deform when exposed to fire, have a curved thin layer, a slight burning smell of coke, are non flammable, and soften when exposed to fire.
PVDF polyvinylidene fluoride
(1) Homopolymer of vinylidene fluoride (VDF).
(2) Advantages: It has excellent corrosion resistance, stain resistance, weather resistance, and resistance to ultraviolet radiation. It can be used for radiation crosslinking to improve mechanical properties. Usually used as coatings and chemical pipelines, chemical parts, and containers in villages. However, PVDF has good mechanical properties and its high carbonization rate when exposed to high heat makes it non flammable. Therefore, it can also be used to prepare insulation for low-frequency cables, such as ceiling insulated cables, flame-retardant cables, heating cables, or optical fibers. The specific gravity is about 1.78
UL444.UL1581 Safety requirements: Elongation rate 100% min, tensile strength 3500PSI min
How to identify Teflon materials, which soften and deform when exposed to fire, have a curved thin layer, a slight burning smell of coke, are non flammable, and soften when exposed to fire.
LSZH (Low Smoke Zero Halogen) Low Smoke Zero Halogen Adhesive
(1) Due to its stable physical and chemical properties, PVC has been widely used as an insulation material in the wire industry for the past few decades. However, PVC contains halogens, which release a large amount of toxic smoke and corrosive gases during combustion, directly damaging nature and endangering human life safety. As a result, an escalating number of countries or regions, particularly Europe and Japan, have enacted stringent regulations aimed at progressively phasing out the utilization of PVC, replacing it with halogens free Low smoke halogen-free adhesive (LSOH) with environmentally friendly properties. (2) Advantages: (a) Reducing the emission of toxic smoke, (b) Reducing the concentration of toxic gases, (c) Non corrosive gases.
How to identify LSZH materials with no odor, white smoke, white residual ash dust after combustion, and self extinguishing properties.
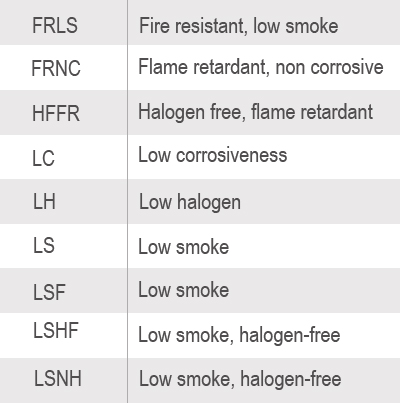
TPE
TPE material: It is a blend type alloy thermoplastic elastomer. In addition to containing SBC basic elasticity, the blending system includes at least one or more other compounding agent components. The types of components depend on the performance requirements of TPE material. With the increasingly widespread application of TPE halogen-free flame-retardant cable materials, there are currently more applications such as mobile phone data cables, earphone cables, industrial cables, automotive cables, military cables, etc. PVC cables will gradually emerge from the world, while TPE will take pride in the world.
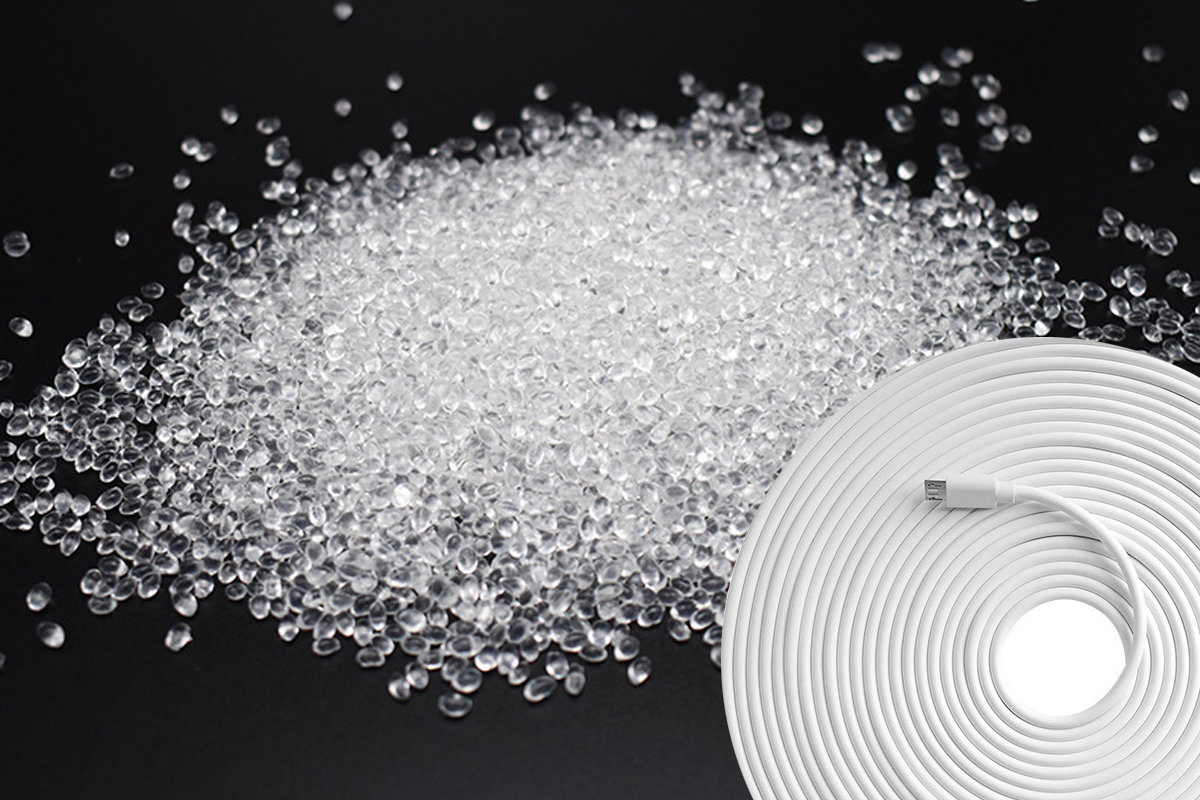
TPV
TPV materials: The development and application of EPDM/PP blended thermoplastic elastomers have gone through three stages, from simple blending to partial dynamic cross-linking blending (TPO) and then to complete dynamic cross-linking blending (TPV). The use of dynamic vulcanization method to fully crosslink EPDM/PP (TPV) has superior strength, high-temperature mechanical strength, heat resistance, and good compression permanent deformation and elasticity compared to traditional TPO, greatly expanding the application range of EPDM/PP thermoplastic elastomers. This series of products can be widely used in automotive interiors and exteriors, sealing systems, covers, engine compartment components, gaskets, building sealing systems, electronic appliances Daily consumer goods and other industrial and civilian fields that require flexibility and consistency. This series of products can be processed on injection molding machines, extruders, and blow molding equipment, and can be fully recycled.
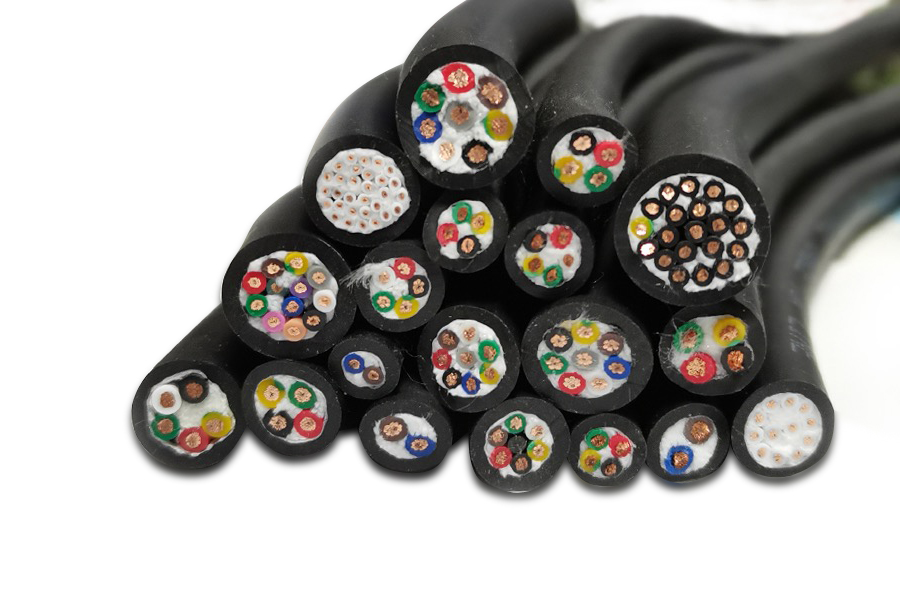
TPO
TPO material: TPO refers to polyolefin thermoplastic elastomer, composed of rubber and polyolefin. Polyolefin thermoplastic elastomer (TPO) is the fastest-growing variety in TPE, composed of rubber and polyolefin. Usually, the rubber component is EPDM, nitrile rubber (NBR) or butyl rubber, and the polyolefin component is mainly PP, PE, or EVA. Currently, the fastest developing is EPDM/PP thermoplastic elastomer. The production process of TPO has gone through simple mechanical blending, partial dynamic vulcanization blending, and then developed into dynamic fully vulcanized blends. The mechanical mixing method is the earliest and most mature production process developed, with a rubber component content of 20% to 30% in the TPO produced. It is mainly used for automotive bumpers and household electrical components. In the TPO produced by dynamic full vulcanization method, the rubber component content is as high as 60%~70%. The product has excellent dynamic fatigue resistance, good wear resistance, ozone resistance, and weather resistance, high tear strength, small compression deformation and permanent deformation. Its comprehensive performance is better than that of EPDM vulcanized rubber, and it is easy to process. It can produce products that can replace thermosetting vulcanized rubber at a lower production cost, and has a strong competitive advantage. TPO has excellent weather resistance, ozone resistance, UV resistance, as well as good high temperature and impact resistance. It has the advantages of simple processing, low cost, continuous production, and other thermoplastic elastomers, and is widely used in fields such as automobiles, electronics, industrial components, and daily necessities. Especially in automotive components, TPO has the largest market, with excellent weather resistance, low density, processing flexibility, and low cost, making it widely used in air valves, bumper sheaths, mudguards, weather resistant sealing strips, mesh windows, rubber strips, conduits, sealing washers, and automotive interior decoration parts. With its excellent electrical performance, water resistance, and ozone resistance, TPO has replaced PVC and partially vulcanized rubber in many occasions, such as flexible cords Booster cables, instrument cables, and low-voltage sheaths. Because the material itself has good designability, processing performance, sealing effect, excellent water resistance and ozone resistance, its performance is no less than that of traditional thermosetting rubber. At present, the application direction of TPO is developing towards the construction field, including civil and industrial buildings, especially the door
and window seals, building expansion joint of large urban buildings, roof materials, waterproof materials, The application of TPO in waterproof rolls is a new field of its application. Currently, this material is used in the cable market for special application scenarios, such as underground humid environments and special environments for underwater operation. Currently, most cable accessory manufacturers internationally use this material.
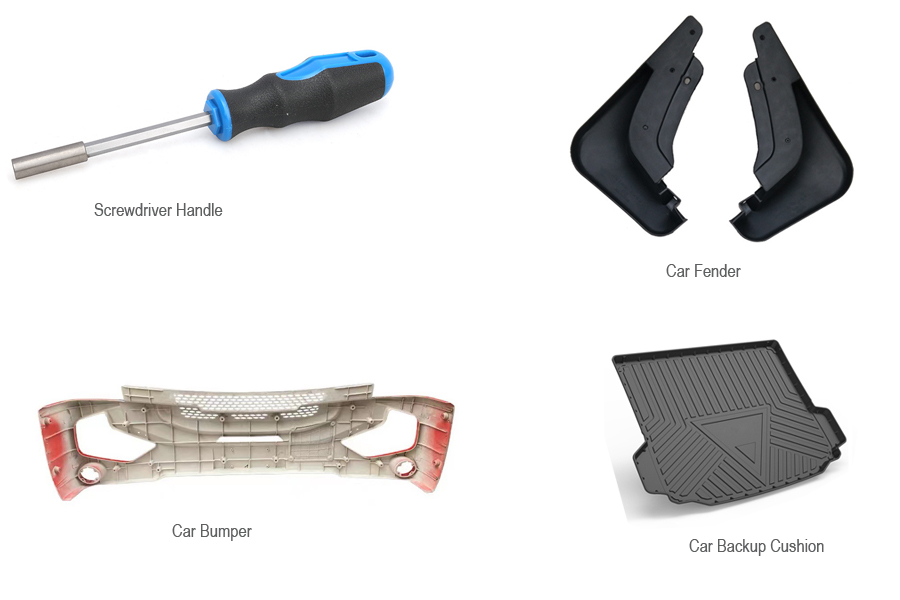
At present, the main function of cables in the market is to transmit signals, electricity, control installation, and connect equipment, and they are the main carriers of cable transmission. It plays an important role in our daily lives, and the existence of electricity makes our lives more convenient and comfortable. There are many types of cables in the market, and one of their main distinguishing methods is materials. Under the leadership of high-frequency, high-speed, and environmental protection, special application materials will also emerge one after another. The above are the current mainstream materials for everyone to refer to.