Types and Applications of Cable Shielding Materials
What are the common shielding materials?
When discussing shielding, are you familiar with its purpose? Shielding is a technology that involves the use of specific materials to obstruct or diminish the transmission of electromagnetic energy. It serves as a crucial method for suppressing electromagnetic interference.
Electromagnetic shielding can be broadly categorized into three types: magnetostatic shielding, electrostatic shielding, and high-frequency electromagnetic shielding.
The goal of all these shielding types is to prevent external electromagnetic fields from infiltrating a designated protected area. The underlying principle relies on leveraging the shielding effect to counterbalance the influence of external fields through induction.
However, due to the distinct characteristics of the fields that require shielding, the material requirements and desired shielding effects may vary accordingly.
Aluminum foil Mylar Material
Aluminum foil Mylar is a composite material consisting of soft aluminum foil and polyester film, combined through gravure coating. Once the aluminum foil Mylar reaches maturity, it undergoes cutting and rolling processes. It can be mixed with adhesive and utilized for assembly shielding and grounding purposes after being die-cut. The primary application of aluminum foil Mylar tape is in the disturbance screening of communication cables.
There are various types of aluminum foil Mylar available, including single-sided aluminum foil, double-sided aluminum foil, spread wing aluminum foil, hot melt aluminum foil, aluminum foil tape, and aluminum plastic composite tape. The aluminum layer in these products provides exceptional conductivity, shielding effectiveness, and corrosion resistance, enabling adaptation to diverse requirements within different ranges. The shielding range typically spans from 100K to 3GHz.
In the case of hot melt aluminum foil Mylar, a layer of hot melt adhesive is coated on the contact surface between the aluminum foil and the cable. Through high-temperature preheating, the hot melt adhesive securely wraps around the cable core insulation, thereby enhancing the cable’s shielding performance. On the other hand, ordinary aluminum foil lacks viscosity, and merely wrapping it around the cable core insulation would result in inadequate shielding performance for the cable.
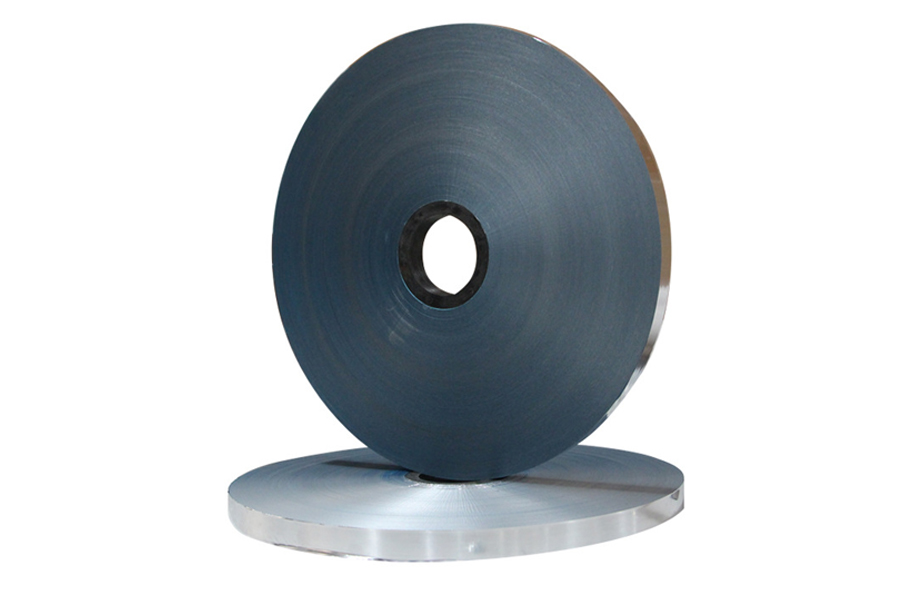
Features and application areas
Aluminum foil Mylar primarily serves the purpose of shielding high-frequency electromagnetic waves. Its main objective is to prevent the contact between high-frequency electromagnetic waves and the cable’s conductor, which could lead to the generation of induced currents and increased crosstalk. When high-frequency electromagnetic waves encounter aluminum foil, Faraday’s law of electromagnetic induction comes into play. The electromagnetic waves tend to adhere to the surface of the aluminum foil, resulting in the generation of induced currents. To prevent interference with the transmission signal caused by these induced currents, a conductor is required to guide them into the ground.
For wire materials utilizing aluminum foil as the shielding layer, it is generally recommended that the aluminum foil has a repetition rate of no less than 25%. Currently, the most prevalent application of aluminum foil Mylar is in network cabling, particularly in environments such as hospitals, factories, and other locations with strong electromagnetic radiation or a significant presence of powerful electrical equipment. Additionally, it finds use in areas where network security requirements are particularly high, such as government institutions.
Copper/aluminum magnesium gold wire mesh (metal shielding) Material
Metal shielding is created by weaving metal wires with specific weaving structures using weaving equipment. The commonly used shielding materials include copper wire (tinned copper wire), aluminum alloy wire, copper-clad aluminum, copper tape (copper-plastic tape), aluminum tape (aluminum-plastic tape), steel tape, and other materials, which correspond to different metal weaving structures. Different structural parameters result in varying shielding properties.
The shielding effectiveness of the woven layer depends not only on the conductivity and magnetic permeability of the metal itself but also on factors such as the number of layers, coverage area, and weaving angle. Generally, a greater number of layers, larger coverage area, and smaller weaving angle contribute to better shielding performance of the woven layer. It is recommended to control the weaving angle within the range of 30-45°. For single-layer weaving, the coverage rate should exceed 80% to effectively convert electromagnetic energy into other forms, such as thermal energy and potential energy, through mechanisms like hysteresis loss, dielectric loss, and resistance loss. This conversion helps consume unnecessary energy and achieve the desired effect of shielding and absorbing electromagnetic waves.
The woven mesh used in metal shielding is typically made of tinned round copper wire or aluminum-magnesium-gold wire. Its primary purpose is to counter low-frequency electromagnetic wave interference, employing the same working principle as aluminum foil. When using woven mesh for shielding cables, it is important to ensure a mesh density of at least 80%. This type of woven mesh is primarily used for laying numerous network cables within the same conduit, reducing external crosstalk between multiple network cables. Additionally, it can be employed for shielding between pairs of cables, increasing the twisted length of the pair and minimizing the requirements for cable separation distance.
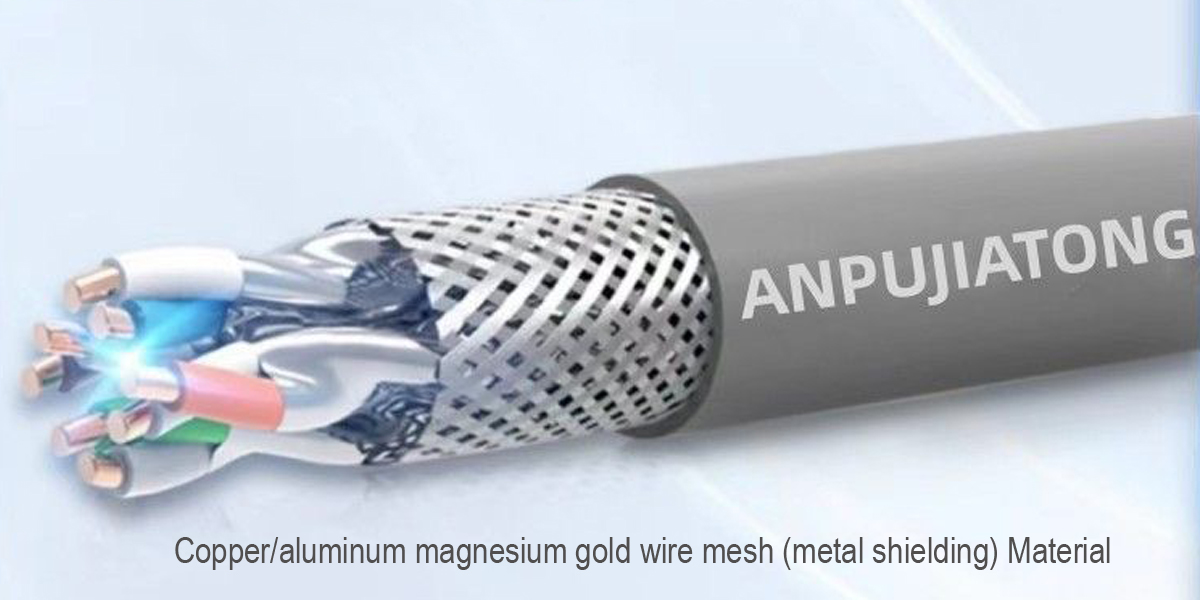
Types and Applications of Cable Shielding Materials
There are two primary types of cable shielding materials. The first type, commonly known as semi-conductive polymer materials, exhibits a certain level of shielding performance within a specific range of resistivity. These materials are classified based on their internal conductive principles. Materials with inherent conductivity are referred to as structural types, while those achieving shielding through fillers are known as composite types. Both structural and composite semi-conductive polymer materials are extensively used as shielding materials in cable structures. This is because semi-conductive polymer materials not only provide electromagnetic interference shielding but also possess robust resistance to various environmental factors, particularly lightning strikes. Consequently, they find widespread application in specialized scenarios such as aircraft cables. The production process for semi-conductive polymer materials is complex and costly, resulting in higher expenses associated with these materials.
The second type of cable shielding material is metal wire braiding. It involves utilizing metal wire as the primary material to form a shielding network that effectively mitigates magnetic interference. In cables requiring shielding, such as HDMI2.1 and USB4 cables, tinned copper wire is commonly employed for weaving the shielding material. The selection of this material aims to enhance the cable’s shielding performance. The design structure and weaving density of the metal wire braid used in cables may vary based on the intended application scenarios. Generally, multi-layer weaving exhibits better performance than single-layer weaving, and the coverage area is inversely proportional to the weaving angle. In other words, to improve the shielding effectiveness, it is necessary to reduce the weaving angle and increase the coverage area. In summary, the effective implementation of metal wire shielding can significantly mitigate electromagnetic interference.
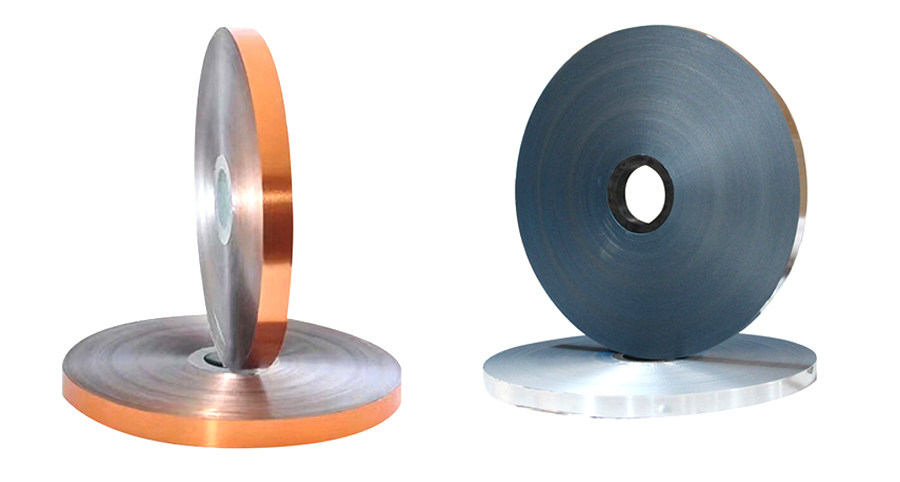
Low-frequency cables constitute a significant portion of cable manufacturing. When cables with different frequencies encounter multiple grounding points, they tend to generate higher levels of noise currents. This situation hinders the achievement of effective anti-interference effects across the entire shielding layer. Adopting a single-point grounding method requires ensuring that the current within the shielding layer cancels itself out, thus confining the interference current within the shielding layer and effectively preventing electromagnetic interference. However, due to the external grounding method of application components, some cables often employ a two-point grounding method for internal shielding. The two-point grounding method allows the return current from the magnetic field inside the cable to exit, thereby reducing the intensity of current interference.
In high-frequency cables, the issue of stray capacitance is more likely to arise, significantly affecting the normal transmission of current in such cables. However, neither the single-point grounding nor the two-point grounding methods effectively address this problem. Therefore, the use of multi-point grounding shielding is recommended for high-frequency cables. In high-frequency cables, multiple frequencies and concentrated surface interference currents exist within the line, which directly amplifies the interference effect, hindering the normal operation of the entire system. By employing the multi-point grounding method, the impedance within the shielding layer is reduced, mitigating the interference caused by noise currents and improving the overall shielding effectiveness.